Failure Analysis su girante
RUBRICA | Come si è rotto? #07TEC EUROLAB
#07
Failure Analysis su Girante
NUOVA RUBRICA | Come si è rotto?
L’oggetto
Una girante è un componente meccanico utilizzato principalmente nelle pompe e nelle turbine. Si tratta di una parte rotante all’interno di un alloggiamento che è progettata per generare flusso o movimento all’interno di un fluido (liquido o gas) o per trasferire energia da una sorgente motrice all’ambiente circostante.
Quando utilizzata all’interno di una pompa, la girante è responsabile della creazione di pressione o flusso nel liquido pompato. Le pompe centrifughe, ad esempio, utilizzano giranti per aumentare la pressione dell’acqua o il flusso di liquido.
Questi componenti possono andare incontro a varie modalità di failure:
- Usura: Nel corso del tempo, la girante può subire usura a causa del continuo contatto con il fluido. Questo può portare a una riduzione delle prestazioni o a una diminuzione dell’efficienza.
- Erosione: Se il fluido pompato contiene particelle abrasive, la girante può erodersi nel tempo, compromettendo le sue capacità di pompare o convertire l’energia.
- Corrosione: L’esposizione a fluidi corrosivi può causare danni chimici alla girante, indebolendola e riducendo la sua durata.
- Stallo o surging: In alcune situazioni, una girante può entrare in stallo o sperimentare surging quando il fluido fluisce in modo non uniforme attraverso di essa. Ciò può causare danni strutturali o ridurre l’efficienza.
- Surriscaldamento: In applicazioni ad alta velocità, il surriscaldamento della girante dovuto a una cattiva lubrificazione o a un design inadeguato può portare a deformazioni o rotture.
- Squilibrio: Un’eventuale perdita di equilibrio nella girante può causare vibrazioni indesiderate, che a loro volta possono portare a guasti o rotture.
Scopo dell’indagine
La girante oggetto d’analisi ha subito una frattura in corrispondenza di una delle palette con superficie di frattura orientata lungo due differenti piani di cui il primo trasversale al condotto della girante, mentre il secondo è tangente alla parete della paletta stessa. Scopo dell’indagine è indagare approfonditamente la tipologia di rottura, caratterizzandone le superfici per determinare i meccanismi di cedimento e formulare ipotesi sulle possibili cause che hanno portato al danneggiamento.
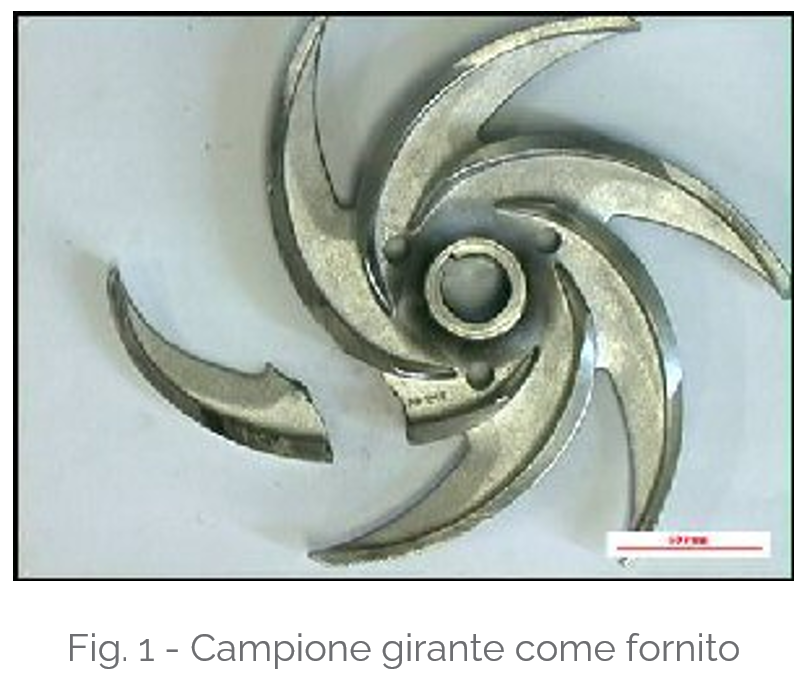
Il campione in esame è costituito da una girante mostrata in Figura 1, che ha subito una frattura in corrispondenza di una delle palette.
La superficie di frattura è orientata lungo due differenti piani di cui il primo trasversale al condotto della girante, mentre il secondo è tangente alla parete della paletta stessa, come evidenziato nella Figura 2.
In particolare il secondo tratto si origina in corrispondenza del raggio di raccordo tra parete verticale e superficie di base del condotto e si unisce alla prima porzione a circa 30mm dall’inizio del condotto stesso terminando in corrispondenza del raggio di raccordo orizzontale a piede paletta.
Le analisi
Oltre alla verifica della composizione chimica del materiale utilizzato per la realizzazione del componente, l’attività analitica si è focalizzata sul caratterizzare il materiale in prossimità della frattura, identificandone la microstruttura e formulando ipotesi sui possibili meccanismi di cedimento mediante indagine frattografica.
L’esame della superficie di frattura mette in evidenza la presenza di una macro morfologia liscia e caratterizzata da linee di spiaggia convergenti verso due punti che si possono notare nella Figura 2. Tale parte di superficie interessa tutta la seconda porzione di area danneggiata, mentre il resto della zona di frattura risulta di aspetto opaco e più irregolare.
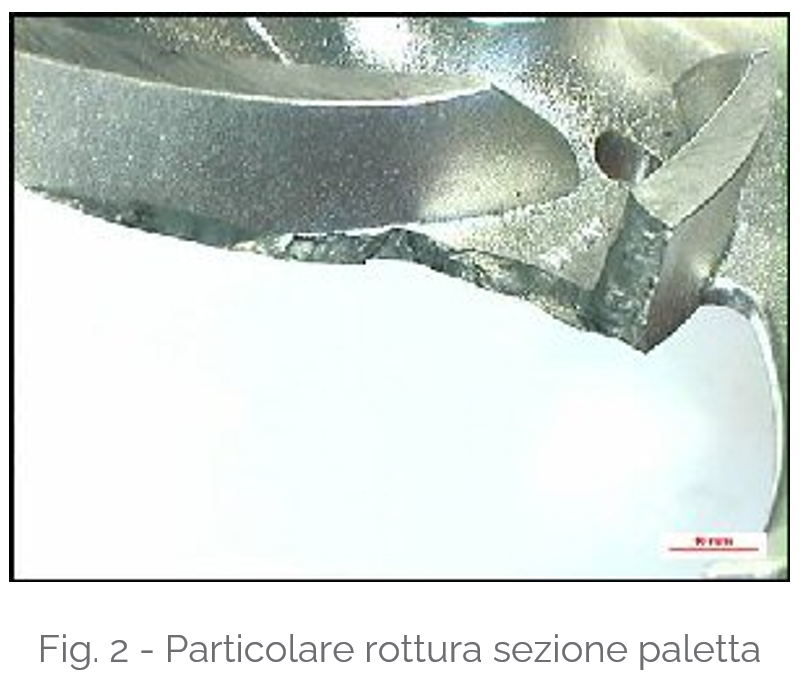
La porzione piana della superficie di frattura presenta una morfologia transgranulare piatta sulla quale emergono evidenti due famiglie di striature convergenti verso due diversi punti.
I punti di origine si caratterizzano per la presenza di cavità che creano discontinuità nel materiale.
La porzione orizzontale della superficie di frattura presenta una morfologia di tipo transgranulare mista caratterizzata da microdimples e porzioni interessate da clivaggio. Tali morfologie sono tipiche di un cedimento di schianto.
La microstruttura rilevata sul campione sulla paletta fratturata è mostrata nella micrografia n°1.
Si osservano isole di fase ferritica disperse in matrice austenitica con percentuale di ferrite intorno al 15%.
Non si rilevano fasi secondarie e precipitati a bordo grano.
La superficie di frattura in corrispondenza delle origini ha un profilo liscio e regolare come mostrato nella micrografia n°2, e la microstruttura risulta analoga al resto del campione.
La micrografia n°3 descrive la struttura rilevata su una paletta non danneggiata.
Si osservano ancora isole ferritiche in matrice austenitica, analogamente alla paletta danneggiata.
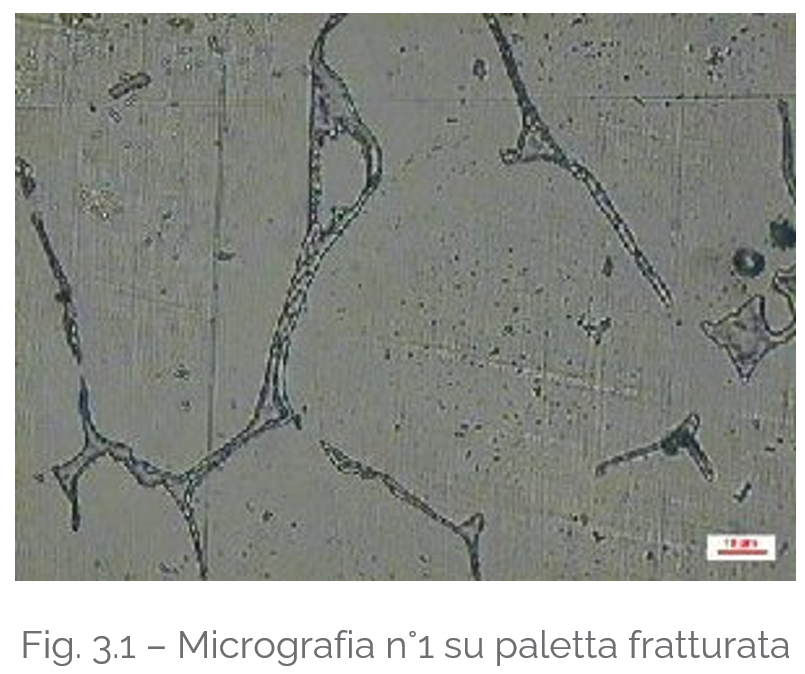
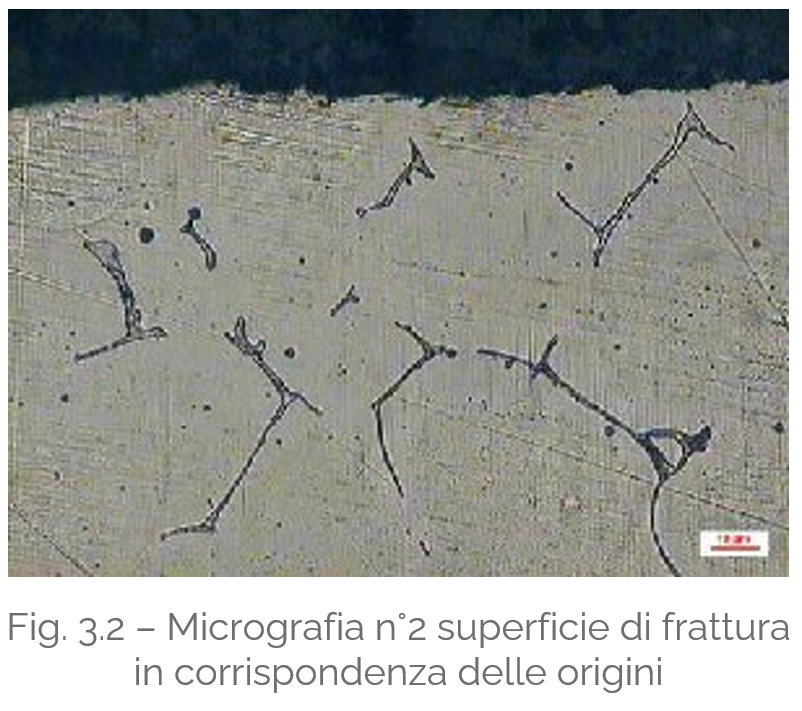
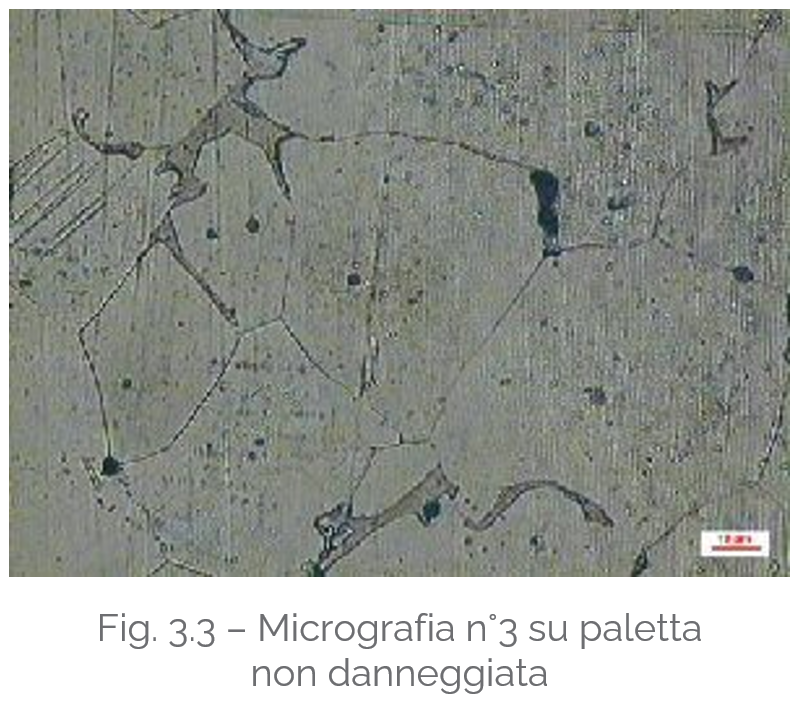
Risultati
Il materiale con cui è realizzata la girante fratturata è classificabile come un acciaio inossidabile da getti del tipo A351 CF3M (SAE 316L), seppure il suo tenore di Cr sia leggermente inferiore al valore minimo della forcella prevista. Lo studio della superficie di frattura indica che la rottura è avvenuta per fatica, con individuazione di due differenti punti di origine, localizzati in corrispondenza del raggio di raccordo tra la parete verticale della paletta e la superficie di fondo condotto. Le tensioni di innesco della cricca di fatica sono di apertura del condotto (concordi alla forza centrifuga).
La densità di striature indica che il ciclo di carico a cui era sottoposta la paletta era di ampiezza modesta. La propagazione interessa tutta la parte di superficie di frattura tangente al profilo della paletta, mentre la parte di superficie ortogonale al condotto costituisce la parte interessata dal cedimento di schianto, avvenuto in modo fragile. La microstruttura del campione è conforme al materiale impiegato e non sono state rilevate fasi anomale. L’esame dei punti di origine mette in risalto soltanto la presenza di microcavità che possono aver favorito la rottura ma che non si ritiene ne siano la causa principale. Date le caratteristiche della frattura e la posizione della superficie danneggiata si ritiene che la nucleazione della cricca sia da attribuire alla concentrazione di tensioni che si è venuta a creare in corrispondenza del piede della pala per cause di tipo geometrico (raggio di raccordo troppo piccolo, a differenza di altre zone in cui tale parte è maggiormente raccordata).
Conclusioni
La frattura della girante è avvenuta per fatica. Il fattore principale di innesco è costituito dal raggio di raccordo a piede pala troppo piccolo che ha determinato una forte concentrazione di sforzi.
Vuoi scoprire perchè il tuo componente si è rotto?
Compila il form e sarai ricontattato dal nostro staff tecnico
Leggi gli altri case study sulla Failure Analysis
Failure Analysis su tubo di gomma
Nuovo caso di analisi failure approfondita su un tubo di gomma
Failure Analysis su valigia da viaggio | Rubrica come si è rotto? #09
Come si è rotta una valigia da viaggio? Nuovo case study di failure analysis
Failure Analysis su Perno filettato | Rubrica Come si è rotto? #08
Nuovo case study di Failure Analysis. Scopriamo come si è rotto un perno filettato
Il tuo componente si è rotto in esercizio e vuoi capire qual è la causa della rottura?