Failure Analysis su braccetto di transpallet
RUBRICA | Come si è rotto? #03TEC EUROLAB
#03
Failure Analysis su braccetto di transpallet
NUOVA RUBRICA | Come si è rotto?
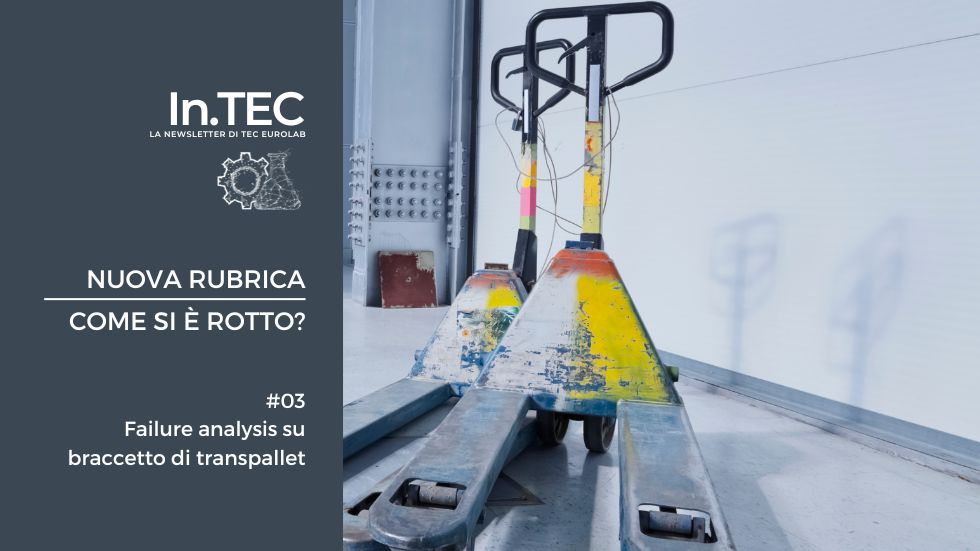
L’oggetto
Un transpallet è un attrezzo di movimentazione utilizzato per il sollevamento e il trasporto di merci su pallet. È composto da una base con ruote e da due bracci metallici che si inseriscono sotto il pallet per sollevarlo.
Le possibili modalità di failure del braccetto di un transpallet includono:
- rottura per sovraccarico: se il braccetto è sottoposto a un carico superiore alla sua capacità di resistenza, può rompersi;
- deformazione plastica: l’uso ripetuto o un carico eccessivo possono causare una deformazione permanente del braccetto, riducendo la sua capacità di sollevamento e trasporto;
- usura e corrosione: l’attrito e l’esposizione ad agenti corrosivi possono causare l’usura del braccetto o la formazione di fessure che possono portare alla sua rottura;
- difetti di fabbricazione o materiali di scarsa qualità: difetti nella progettazione o nella fabbricazione del braccetto, o l’uso di materiali di scarsa qualità, possono comprometterne la resistenza e la durata nel tempo;
- mancanza di manutenzione: la mancanza di lubrificazione, pulizia o ispezioni regolari può favorire l’accumulo di sporco, corrosione o danni invisibili che possono portare a failure impreviste del braccetto.
Scopo dell’indagine
Lo scopo dell’indagine è analizzare il danneggiamento avvenuto a carico del componente. Non sono state fornite informazioni relative al materiale o allo stato di fornitura del manufatto. Il danneggiamento consiste nella rottura del componente in corrispondenza della saldatura con il tubolare.
Le analisi
L’osservazione delle zone di rottura mostra l’assenza di deformazione plastica e la presenza di superfici di frattura brillanti e frastagliate. Questi aspetti macroscopici indicano una modalità di rottura fragile. Le superfici di frattura sono state analizzate tramite microscopio elettronico a scansione per valutarne le caratteristiche morfologiche di rottura.
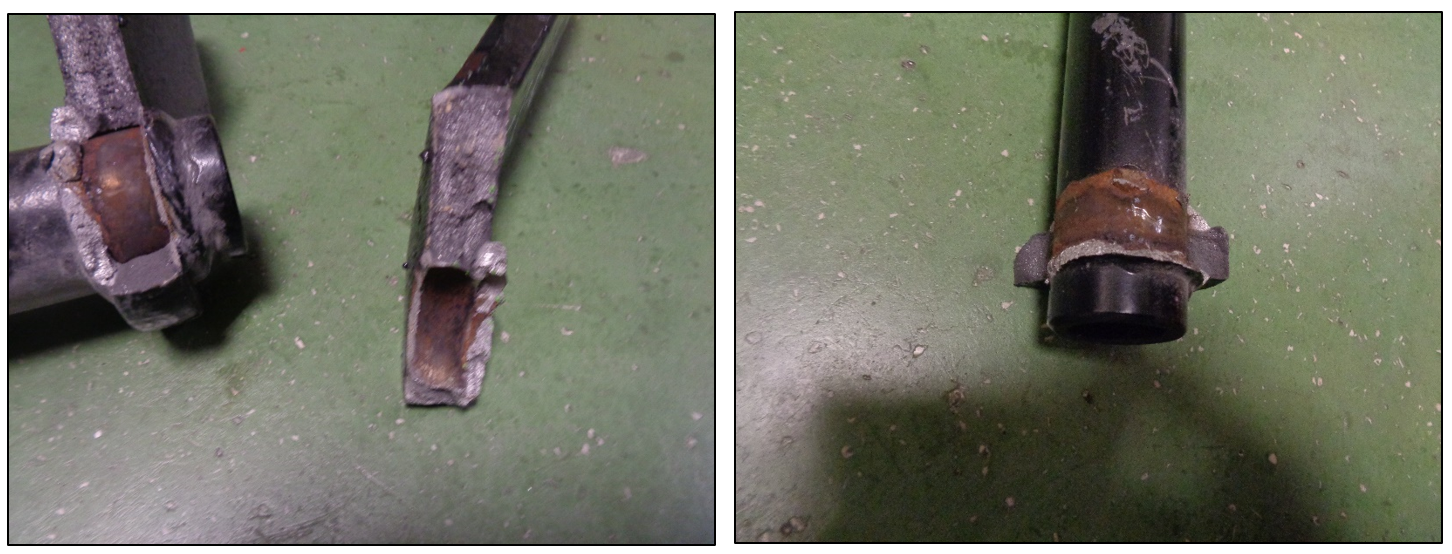
Fig. 1 – Esame visivo
L’osservazione frattografica delle superfici di rottura ha rivelato la presenza di difetti di integrità, come ritiri interdendritici, nella zona di fusione. La morfologia del danneggiamento è caratterizzata da un clivaggio, indicando una rottura per schianto con modalità fragile. Inoltre, la superficie di rottura nella zona di saldatura mostra distacchi colonnari, anch’essi tipici di rotture fragili.
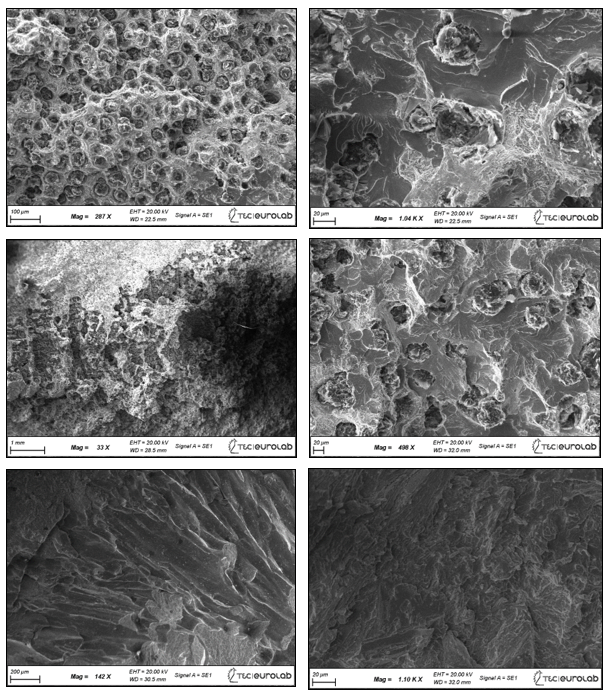
Fig. 2 – Morfologia
L’analisi chimica mostra la composizione del materiale, che corrisponde a una ghisa sferoidale del tipo EN-GJS-500-7 secondo la normativa UNI EN 1563:2018.
I valori di resistenza a trazione sono conformi a quanto ci si aspetta per un materiale di questo tipo, confermando la classificazione come ghisa sferoidale EN-GJS-500-7.
L’esame metallografico rivela la presenza di ritiri interdendritici di grandi dimensioni e una cricca nella zona fusa della saldatura. La microstruttura consiste in una matrice ferritico-perlitica nella ghisa e martensite aciculare nella zona fusa.
La durezza Brinell a cuore è di 187 HBW, mentre la durezza Vickers varia da 693 HV a 716 HV nelle diverse zone analizzate.
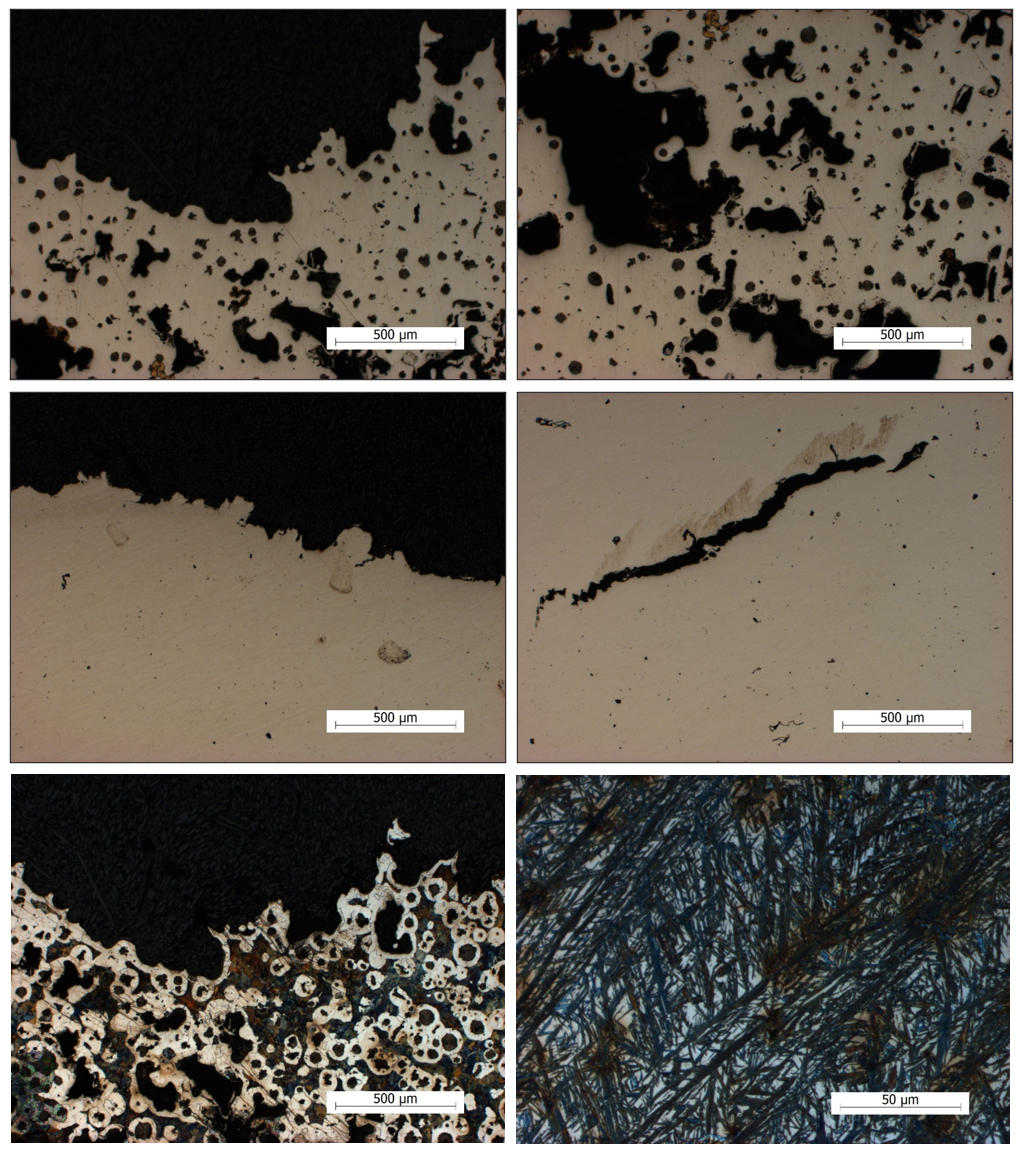
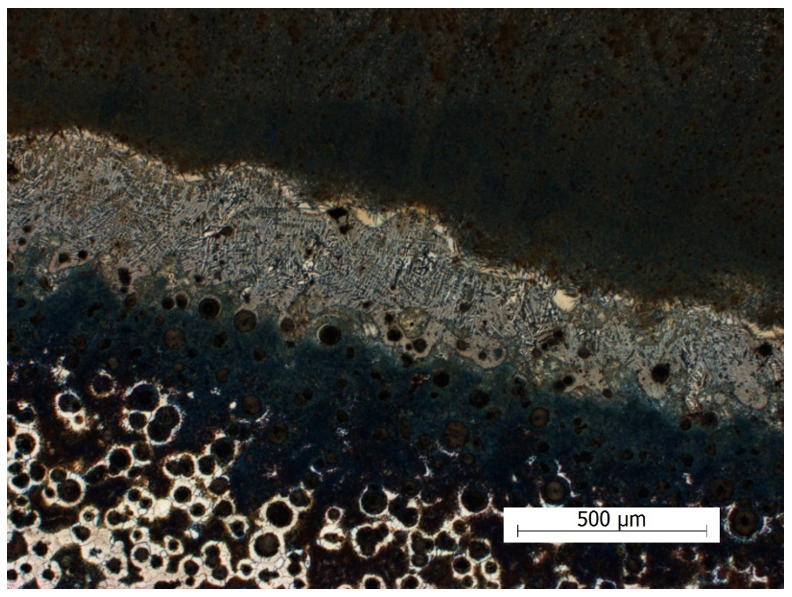
Fig. 3 e 4 – Microstruttura
I risultati
Come evidenziato in fase analitica, il materiale del componente fratturato è una ghisa sferoidale del tipo EN-GJS-500-7 secondo la normativa UNI EN 1563:2018. La rottura è avvenuta in modo fragile e di schianto, come confermato dall’esame visivo e frattografico.
L’origine del cedimento è attribuibile a due problematiche. In primo luogo, la saldatura è stata eseguita senza pre-riscaldo e post-riscaldo, causando una struttura dura e fragile nella zona saldata. Questo ha reso la zona suscettibile alla rottura sotto carichi normali. Inoltre, sono stati riscontrati difetti di integrità dovuti a ritiri interdendritici durante la solidificazione, riducendo la sezione resistente del componente e favorendo la rottura anche con carichi inferiori a quelli standard.
Conclusioni
Il cedimento del componente è attribuibile a due problematiche distinte:
- i difetti di integrità nella fusione in ghisa, che hanno causato una significativa riduzione della sezione resistente;
- la saldatura, effettuata senza considerare la temprabilità dei materiali, risultando in un giunto estremamente duro e fragile.
Si consiglia quindi di verificare la qualità interna della fusione e di adottare un materiale d’apporto appropriato e procedure di pre-riscaldo e post-riscaldo durante il processo di saldatura.
Vuoi scoprire perchè il tuo componente si è rotto?
Compila il form e sarai ricontattato dal nostro staff tecnico
Leggi gli altri case study sulla Failure Analysis
Failure Analysis su tubo di gomma
Nuovo caso di analisi failure approfondita su un tubo di gomma
Failure Analysis su valigia da viaggio | Rubrica come si è rotto? #09
Come si è rotta una valigia da viaggio? Nuovo case study di failure analysis
Failure Analysis su Perno filettato | Rubrica Come si è rotto? #08
Nuovo case study di Failure Analysis. Scopriamo come si è rotto un perno filettato
Il tuo componente si è rotto in esercizio e vuoi capire qual è la causa della rottura?